カウンター
カレンダー
アーカイブ
プロフィール
HN:
TWINKLING STAR
年齢:
48
HP:
性別:
男性
誕生日:
1976/01/18
職業:
普通の会社員
趣味:
最近は写真
リンク
カテゴリー
最新記事
(08/17)
(03/16)
(03/14)
(02/09)
(01/27)
(01/25)
(01/22)
(01/17)
(01/16)
(01/12)
アクセス解析
RSS
FX NEWS
-外国為替-
2024.05.05 Sun 15:55:31
×
[PR]上記の広告は3ヶ月以上新規記事投稿のないブログに表示されています。新しい記事を書く事で広告が消えます。
2011.02.09 Wed 06:26:45
2つくらい前にR-Mapにおけるリスクの低減を書きました。
今度はR-Mapによる事故対応判断をどうするかです。
販売前の製品安全の判断をR-Map上で行うのであれば、販売開始後の市場で起きた製品事故もR-Map上で判断しないとおかしいですもんね。
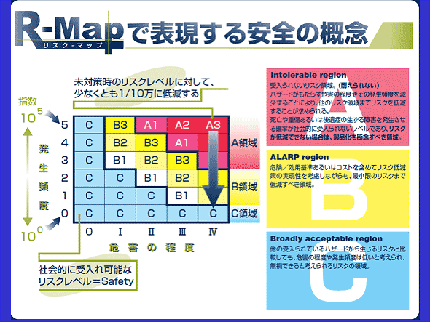
詳しくは、日科技連のサイトを御覧ください。
市場で起きた製品事故をR-Map上で判断させようとしたとき、重要なのは発生頻度ゼロレベル(最下部のC領域)をどう決めるかということ。
例えば、ゼロレベルの発生確率を「1億分の1」(10-8乗)とした場合、市場における稼働台数100万台の製品が100年間事故が起きないレベルがゼロレベルということになります。
どうやら消費生活用製品はこれくらいの頻度を設定するようです。
市場の事故情報の取扱いを簡単に言うと、
A領域:リコールすんぞ
B領域:対策すんぞ
C領域:なにもしない
って感じ。実際はこんなにスッパリ割り切れないけどね。
ゼロレベルをどう決めるか、候補は2つ。
①消費生活用製品と想定使用者が同じ(要するに不特定多数)であれば、消費生活用製品と同じ10-8乗をゼロレベルとするべき。
②自社製品の市場規模に合わせ、ゼロレベルを設定する。正直、うちの場合は10-7乗でも厳しいくらいかなと。
両方メリット・デメリットがあって、①みたいに厳しく取るとちょっとしたことで「リコールすんぞゴルァ!」ってことになるわけで。
また、②みたいに全体の流れに逆らって緩くしてしまうと結局今と変わらない判断基準(R-Map上は別に対策しなくていいけど、営業がやれって言うからやる・・・みたいな)となっちゃいそうで。
結局、システマチックにプロットすることは可能となるが、ある程度人の気持が入った上での対応判断になるかなっていう落としどころ。
製品対応はまぁコレで何とかなると思う。
もっと大変なのは「事故情報の開示と報告」。これは・・・むぅ。
↓いつもありがとうございます♪



今度はR-Mapによる事故対応判断をどうするかです。
販売前の製品安全の判断をR-Map上で行うのであれば、販売開始後の市場で起きた製品事故もR-Map上で判断しないとおかしいですもんね。
詳しくは、日科技連のサイトを御覧ください。
市場で起きた製品事故をR-Map上で判断させようとしたとき、重要なのは発生頻度ゼロレベル(最下部のC領域)をどう決めるかということ。
例えば、ゼロレベルの発生確率を「1億分の1」(10-8乗)とした場合、市場における稼働台数100万台の製品が100年間事故が起きないレベルがゼロレベルということになります。
どうやら消費生活用製品はこれくらいの頻度を設定するようです。
市場の事故情報の取扱いを簡単に言うと、
A領域:リコールすんぞ
B領域:対策すんぞ
C領域:なにもしない
って感じ。実際はこんなにスッパリ割り切れないけどね。
ゼロレベルをどう決めるか、候補は2つ。
①消費生活用製品と想定使用者が同じ(要するに不特定多数)であれば、消費生活用製品と同じ10-8乗をゼロレベルとするべき。
②自社製品の市場規模に合わせ、ゼロレベルを設定する。正直、うちの場合は10-7乗でも厳しいくらいかなと。
両方メリット・デメリットがあって、①みたいに厳しく取るとちょっとしたことで「リコールすんぞゴルァ!」ってことになるわけで。
また、②みたいに全体の流れに逆らって緩くしてしまうと結局今と変わらない判断基準(R-Map上は別に対策しなくていいけど、営業がやれって言うからやる・・・みたいな)となっちゃいそうで。
結局、システマチックにプロットすることは可能となるが、ある程度人の気持が入った上での対応判断になるかなっていう落としどころ。
製品対応はまぁコレで何とかなると思う。
もっと大変なのは「事故情報の開示と報告」。これは・・・むぅ。
↓いつもありがとうございます♪


PR
2011.01.27 Thu 06:31:50
後工程はお客様
=============
・顧客だけがお客様ではない。後の工程、受け手の全てがお客様。
・自分の工程での責任を果たす。
・前工程は後工程に対して品質の責任がある。
・前工程からは品質のよいものしか受け取らない。
=============
標準化
=============
・仕事のやり方を誰が、いつ実施してもまったく同じやり方でかつ、合理的な方法で実施するその方法を決めること。
国際標準化(ISOなど)
国家標準化(日本工業規格JISなど)
社内標準化(社規、作業標準、手順書など)
品質管理は標準化をすること。
ーコストの削減につながる互換性向上
ー品質の向上
ー技術蓄積
=============
↓いつもありがとうございます♪



=============
・顧客だけがお客様ではない。後の工程、受け手の全てがお客様。
・自分の工程での責任を果たす。
・前工程は後工程に対して品質の責任がある。
・前工程からは品質のよいものしか受け取らない。
=============
標準化
=============
・仕事のやり方を誰が、いつ実施してもまったく同じやり方でかつ、合理的な方法で実施するその方法を決めること。
国際標準化(ISOなど)
国家標準化(日本工業規格JISなど)
社内標準化(社規、作業標準、手順書など)
品質管理は標準化をすること。
ーコストの削減につながる互換性向上
ー品質の向上
ー技術蓄積
=============
↓いつもありがとうございます♪


2011.01.22 Sat 07:54:30
消費生活用製品安全法の改訂がなされ、消費者保護の空気が非常に濃い今日この頃、みなさまいかがお過ごしでしょうか。
あれ、けっこう厄介ですよねぇ。メーカーからしてみると。
家電における製品安全とか、けっこう「過保護すぎないか」とか「そこまでやるのか」っていう感じで受け取っている人もいるんですが、日本って安全に関しては遅れているようですね。欧米ではリスクアセスメントを義務付けていたりするんですが、日本ではそこまでではありません。ただ、最近はリコールや重大製品事故の報告が義務付けられたりしてきているので、かなり変わってきたのかなと。まぁメーカーからしてみると非常に厄介なのですが、義務であれば従わざるを得ません。義務違反のリスクのほうがえらい大きいですしね。
最近、うちでもリスクアセスメント実施を仕掛けています。要するに製品の安全性を高めるための仕組みづくりですね。
・安全設計のガイドラインを決める。
・過去の事故情報を設計部門へ提供する。
・安全性の評価は試作段階から開始する。
・安全性の評価項目を明確にする。
・問題点の大きさ、どの程度の対策が必要か見えるようにする。
全体のフローは別として、だいたいこの5点で構成しました。
で、「問題点の大きさ、どの程度の対策が必要か見えるようにする」ために「R-Map」を用いました。
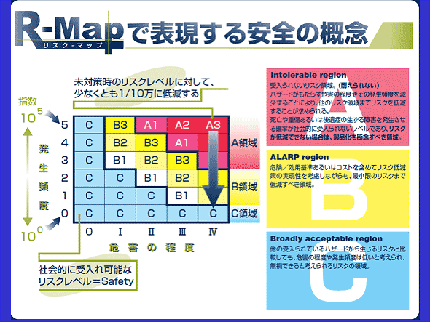
詳しくは、日科技連のサイトを御覧ください。
試作にて抽出された問題点を一番上にプロット(軽傷ならB3、通院ならA1、重傷ならA2、死亡ならA3)し、適切な対策を入れることでC領域まで持っていくというものです。次期新製品に対して取り組み最中ですが、既存製品の流用箇所に対する判断が厄介ですね。新規設計部分に対しては「対策を行う」でOKなんですが、既存製品の流用箇所の場合、以前に安全性OKという判断をしているだけに今更NGと判断して対策させるというのは非常に困難です。問題点であり要対策であるというロジックより現状の生産コストなどが優先され、ある意味計算では計り知れない「上の判断」が優先されているわけです。まぁ、今のところは仕方がないかなと諦めつつも、今後は改善されていくだろうな、と。
設計段階に対する製品安全の取り組みは何とか今期中にある程度軌道に載せられそうで、来期は「市場で発生した事故情報」の判断をR-Map上で行うことを検討します。要するに製品開発段階から販売段階、最期に廃棄されるまでの製品安全に関する事項を一気通貫でR-Map上で判断しようとしているわけです。でないと安全の判断レベルが販売前と販売後で異なるというヘンテコなことになってしまうので、ものさしは一つでないといけません。
来期の方が厄介だろうなぁ・・・。
↓いつもありがとうございます♪



あれ、けっこう厄介ですよねぇ。メーカーからしてみると。
家電における製品安全とか、けっこう「過保護すぎないか」とか「そこまでやるのか」っていう感じで受け取っている人もいるんですが、日本って安全に関しては遅れているようですね。欧米ではリスクアセスメントを義務付けていたりするんですが、日本ではそこまでではありません。ただ、最近はリコールや重大製品事故の報告が義務付けられたりしてきているので、かなり変わってきたのかなと。まぁメーカーからしてみると非常に厄介なのですが、義務であれば従わざるを得ません。義務違反のリスクのほうがえらい大きいですしね。
最近、うちでもリスクアセスメント実施を仕掛けています。要するに製品の安全性を高めるための仕組みづくりですね。
・安全設計のガイドラインを決める。
・過去の事故情報を設計部門へ提供する。
・安全性の評価は試作段階から開始する。
・安全性の評価項目を明確にする。
・問題点の大きさ、どの程度の対策が必要か見えるようにする。
全体のフローは別として、だいたいこの5点で構成しました。
で、「問題点の大きさ、どの程度の対策が必要か見えるようにする」ために「R-Map」を用いました。
詳しくは、日科技連のサイトを御覧ください。
試作にて抽出された問題点を一番上にプロット(軽傷ならB3、通院ならA1、重傷ならA2、死亡ならA3)し、適切な対策を入れることでC領域まで持っていくというものです。次期新製品に対して取り組み最中ですが、既存製品の流用箇所に対する判断が厄介ですね。新規設計部分に対しては「対策を行う」でOKなんですが、既存製品の流用箇所の場合、以前に安全性OKという判断をしているだけに今更NGと判断して対策させるというのは非常に困難です。問題点であり要対策であるというロジックより現状の生産コストなどが優先され、ある意味計算では計り知れない「上の判断」が優先されているわけです。まぁ、今のところは仕方がないかなと諦めつつも、今後は改善されていくだろうな、と。
設計段階に対する製品安全の取り組みは何とか今期中にある程度軌道に載せられそうで、来期は「市場で発生した事故情報」の判断をR-Map上で行うことを検討します。要するに製品開発段階から販売段階、最期に廃棄されるまでの製品安全に関する事項を一気通貫でR-Map上で判断しようとしているわけです。でないと安全の判断レベルが販売前と販売後で異なるというヘンテコなことになってしまうので、ものさしは一つでないといけません。
来期の方が厄介だろうなぁ・・・。
↓いつもありがとうございます♪


2011.01.17 Mon 19:19:26
2010.12.25 Sat 10:23:24